WHAT THE FLUX!
WHY DID MY COFFEE MUG COME OUT OF THE KILN AND LOOK SO DIFFERENT FROM WHAT I EXPECTED?
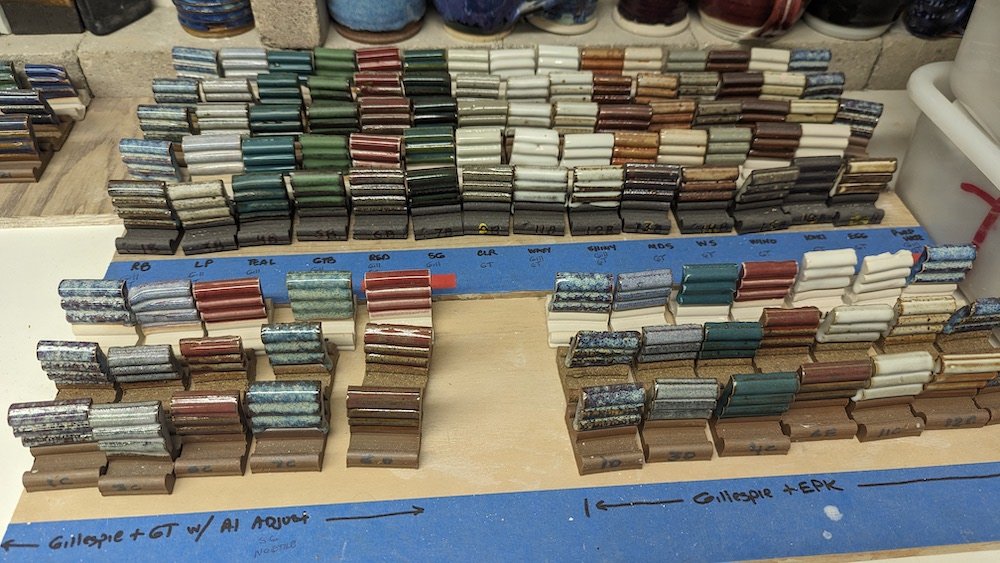
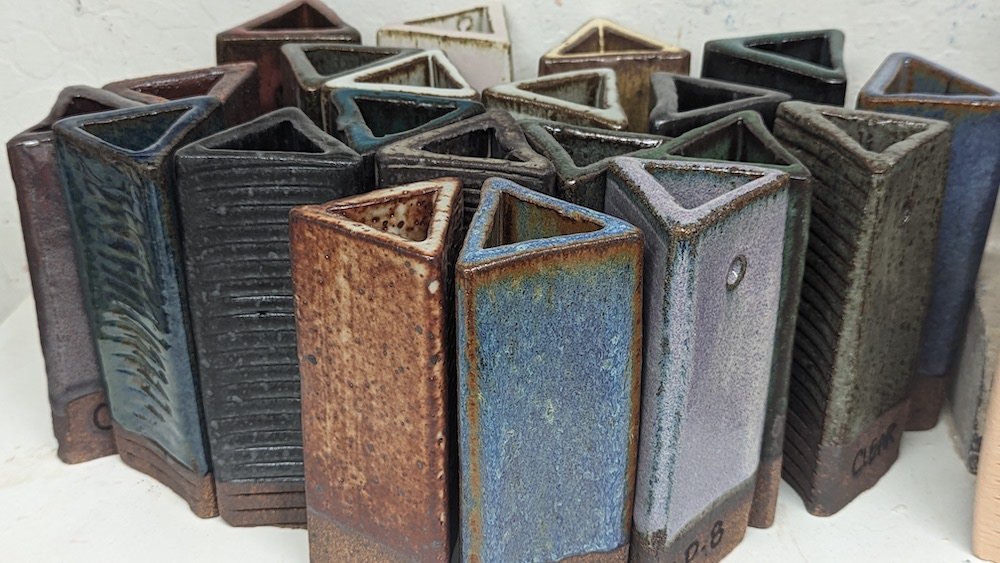
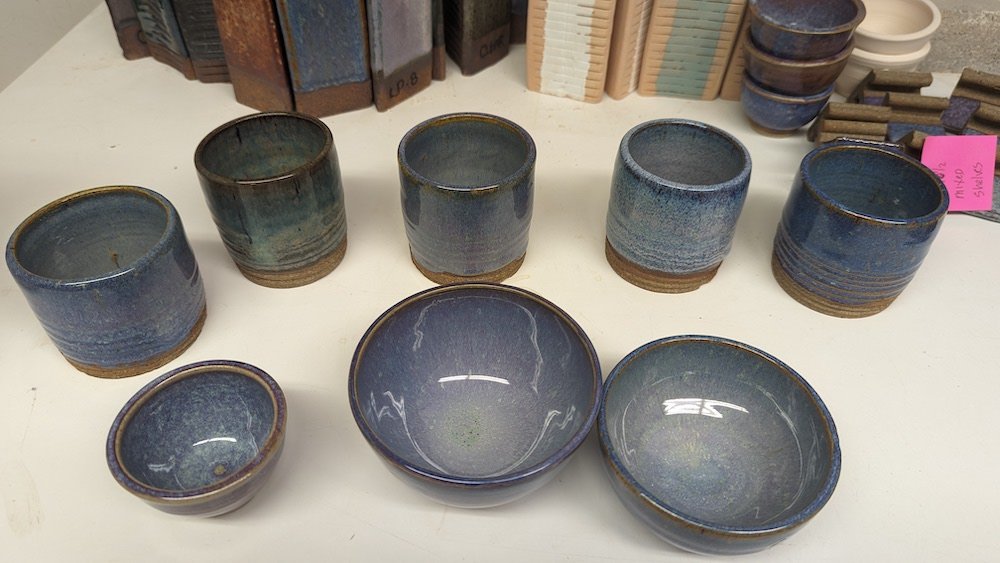
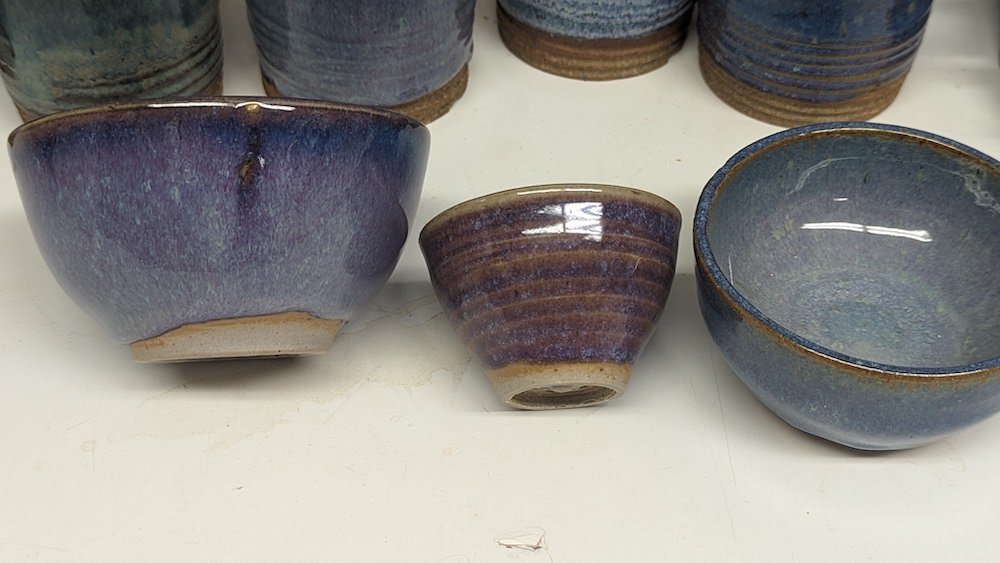
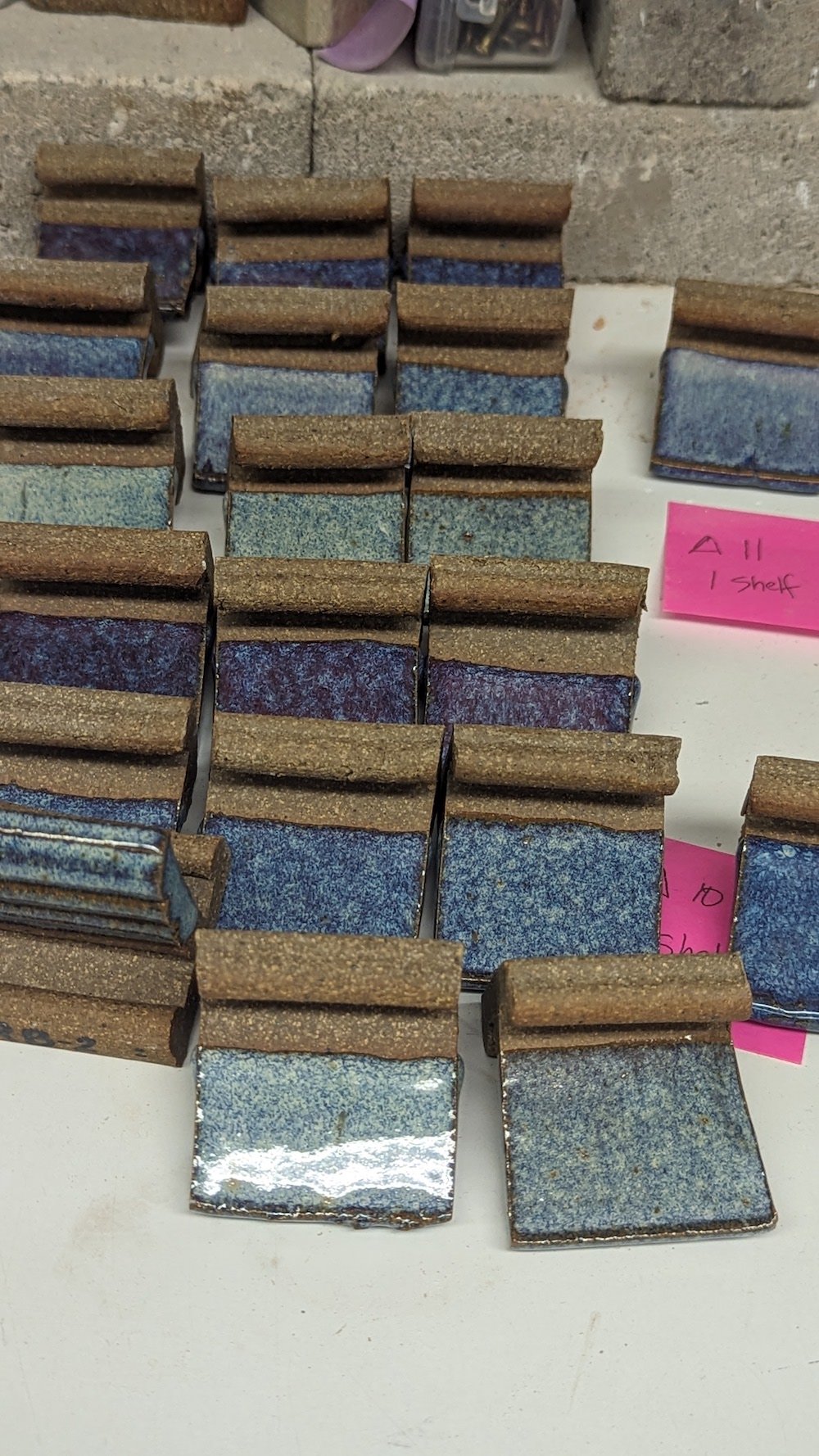
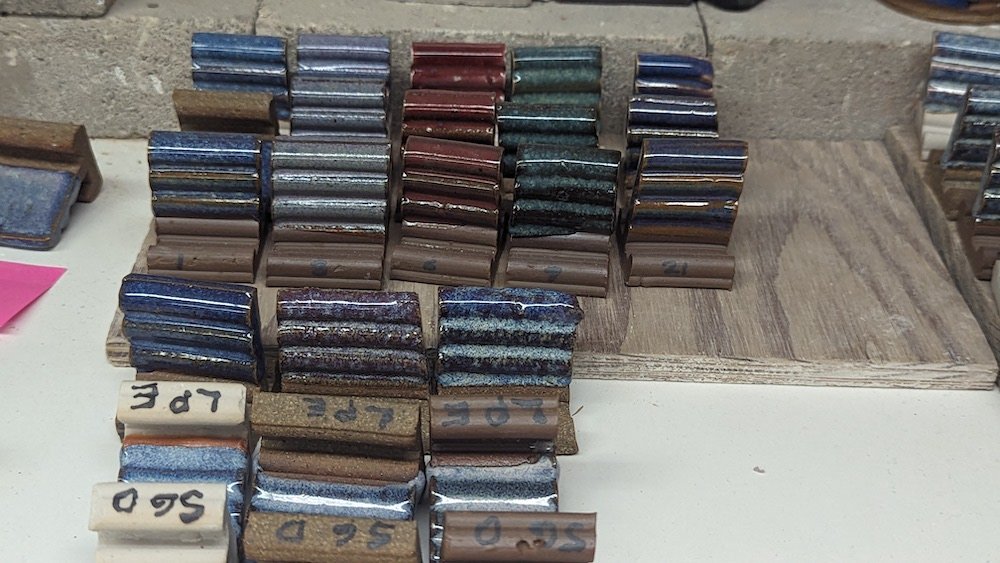
(WTF! June 2024 Edition)
I hear this often as the Glaze Tech for The Potters’ Studio. As a long-time member and for the last few years, staff, I’ve experienced this myself many times.
Usually, cone 10 reduction glazes get classified into the following categories:
Shino Glazes: Malcolm Davis Shino, White Shino. (Shinos depend on soluble soda ash for the color effects, carbon trapping and other effects. Using wax on the outside and delaying pieces for a week on the shelf, change the amount of soda crystals on the outside of the glaze. Soda migrates to the surface over time. Shino glazes can vary so much based on how full the glaze bucket is and how much soda is in the glaze. The heavy clay content sometimes results in some crawling as a feature. Medium reduction with some excess carbon can help with more carbon trapping with sufficient soda at the surface. Usually, results are different every time with Malcolm Davis.)
Phase Separated Glazes: Rusty Blue, Sea Green, Red, Sapphire Blue. (Phase separated glazes contain two different glasses that simultaneously exit in the same glaze. A silica-based glass and a boron-based glass that melt at different temperatures and sometimes have a different color in each. They usually appear with swirls and artifacts of movement in them. Sometimes crystals swirl in one of the glasses. Phase Separation glazes are very sensitive to small changes in silica, alumina, heat, melt viscosity and thickness of glaze application.)
Crystal Forming Glazes: Rusty Blue, Lipstick Purple, Green To Black, Red, Sea Green, St John’s Black, Sapphire Blue, Coleman Khaki, VC Satin Black. (Crystals that form in these glazes are also very sensitive to small changes in silica, alumina, heat, melt viscosity and thickness of glaze application.)
Celadon Glazes: Fraser Blue, Racer (Need to be applied fairly thin and require well-timed reduction for the small amount of iron oxide to change color. Traditionally used on porcelain clay bodies, will look mostly grey on stoneware bodies.)
Stable/Liner Glazes: Teal, Clear, Yellow Salt, Waxy White, Shiny White, Winokur Grey, Eggshell White. (Mostly bulletproof and consistent. You have to work at it to get bad results. Just pay attention to best practices including mixing, dip times, clean bisque, etc.)
All glazes, based on their type above, have different levels of susceptibility to the following variables:
Is the Specific Gravity correct for this glaze? The higher the specific gravity, the more solids will deposit on the bisque. This couples with dipping time. There is an optimal dance between the two. We have selected the best of both to create glazes that apply well.
Was the glaze mixed thoroughly prior to each application? Usually, the water in the glaze floats to the top of the bucket. It’s critical to completely mix the glaze so all the materials are uniform top to bottom. This can take a few minutes.
Are there any floating bits of bisque in the glaze bucket? There’s nothing worse than your piece being ruined by someone else’s bisque bits sticking to your piece while dipping. We provide strainers in the glaze area for you to use or alert staff. We sieve all the glazes when we make a new batch.
Was the piece bisque fired to cone 05? We fire all our electric bisque kilns to 05. If you bisque at home, use a slow fire 05 for consistency. The difference in bisque temperature and speed affects porosity and changes dip times and how much glaze gets deposited on your piece.
Was the piece rinsed, clean of bisque powder or bits and completely dried before glaze application? Bisque dust and bits will contaminate the glaze and affect the application.
Was the piece dipped in the glaze for the right amount of time? Dip times affect how much solids get deposited on the piece. We post the optimal dip time in seconds on the glaze wall based on our testing of 5 different clays on a standard shape. It’s best to keep your own records to see what dip time works best for you based on the clay, the piece thickness, the shape, surface texture, etc.
Did you layer glazes? Layering glazes can be exciting and terrifying. Kiln shelves are expensive! When you layer glazes, you are changing the chemistry. With 20 glazes available, you have 400 different combinations that create 400 new chemistries. This introduces a completely new set of variables and uncertainty into your process. It’s hard enough keeping a single dip consistent with all the possible variables of just a single dip. Even a Stable/Liner glaze like Waxy White can react to a second dip of another glaze on top with catastrophic results. The Magnesium flux is the culprit, it lowers the melt temperature of what’s dipped with it and makes it run wild.
Does your piece have texture or lines trimmed into it? When some glazes pool in low spots or thin on high spots, the glaze can look very different. Our Phase Separated and Crystal Forming glazes are very sensitive to thickness and you can use this in your design aesthetics. Green To Black will not look Green unless it’s thick enough.
What is the shape of your piece? Gravity plays a role in glaze outcome. The shape of your piece and the slope can encourage the glaze to move or pool depending on the shape. Potters like Tom Coleman and Steven Hill create their shapes to take advantage of the glaze properties of their movement at temperature.
Where was the piece put in the kiln? Placement in the kiln can affect glaze outcome for Shino, Phase Separated, Crystal Forming and Celadon Glazes. The kiln temperature can naturally vary 10-15 degrees depending on shelf location, position in the kiln and how the kiln was packed. In a communal kiln, you can’t control these variables. You can when you contract to run your own kiln like our Little Geil.
Was the kiln fired to our standard settings? Our experienced Kiln Firing team has an impressive record of very consistent firing to cone 10 and very consistent medium + reduction that results in the perfect combination of toasty body reduction of iron clays and fully developed color of all our glazes. Proper Reduction amount and timing and temperature have a huge effect on all our glazes except the Stable/Liner glazes. The kiln packs are taken from each firing and put on the glazed pieces rack for you to see.